Timber Frame or cavity wall for house extension – 5 key things to consider
You’re building your house extension, you’ll need to consider whether to make it timber frame, or whether to make it all masonry.
Let’s talk about the pros and cons of both these wall types,….. and…. What I recommend for your own builds ….
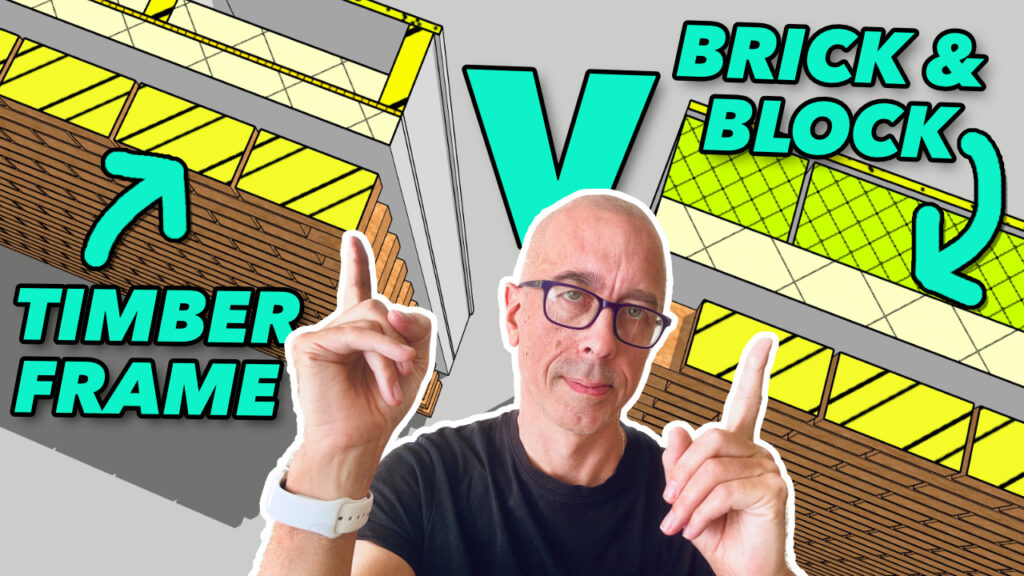
Timber frame v masonry cavity walls for the DIYer
Here’s a typical 3 bedroom house, which we’ve done some work on, it’s a masonry cavity wall with concrete floors, that’s blockwork inner leaf and facing brick outer leaf, can also be blockwork with rendered over the top, can also have with concrete floors.
And…. this house….
This house is timber frame…..…. they both look the same.
So… just because a building’s structure is timber frame, it doesn’t mean it looks any different from masonry cavity.
We always go for a comparison with Cost. But first we need to understand the Materials and Construction for both wall types.
From KingSpan’s website.
Construction of Timber Frame
We’ll start with timber frame wall and how much it costs, breaking it down into elements.
From outside to inside we have:
102mm brickwork.
This is what we call the outer leaf.
It’s that funny size because 102mm is actually 4 inches. The outer leaf is just the cladding, or rain screen.
Ventilated cavity
Then we have a 50mm cavity. 50mm is the minimum size permitted, don’t let anyone persuade you to do it smaller.
This cavity has three purposes,
- it acts as a barrier to moisture
- and as a bit of a thermal barrier, since air is an insulator which can help slow down heat loss.
- The third, the most misunderstood purpose of a cavity, is to form a ventilated void between outside and inside, using perpend vents……See the blue arrows
- See my video here about how ventilating voids will save you from condensation and moisture leakage catastrophes in home builds.
Win the Vapour Barrier War for your Attic extension, Lofts, House Extension and Renovations
Cavity insulation
Next we need our cavity insulation, sitting against the inner leaf. This is the only part of the wall whose thickness can change depending on the level of insulation you require.
How do we get the thickness of our insulation? We can use some online calculators like I’m doing here, U value / R value stuff is so important nowadays to prevent thermal loss through the building envelope.
That sits against a breather membrane stapled to some sheathing, for a house extension, 9mm osb is fine, sheathing stops any horizontal racking of the frame.
For OSB or plywood, because the glue they use is impermeable, I’ll make sure to leave gaps between the sheets to allow the vapour to breathe through to the breather membrane.
Timber studs forming the Timber Frame
…And then, for the inner leaf, we have our structural studs, our timber frame. The inner leaf which is the bit that’s holding the roof and floors up, the loadbearing bit.
For domestic housing studs will be either
- 89 x 38mm treated CLS, or…. usually these days you need to go bigger,
- Choosing up to 145 x 45 graded and treated timber.
- Centres will either be around 400mm or 600mm, depending on loadings
You’ll have your structural engineer to help you with these sizes if you’re doing it to building regulations of you’re in the UK, and I’ve made a video about how to select your timber sizes here.
Timber sizes for your home build, you don’t need a structural engineer
Insulation between studs
We need additional insulation between the studs, leaving us space to run our services on the warm side.
Vapour barrier
Then it’s a vapour barrier, 12.5mm plasterboard sheets to form the shell, and around 3mm of plaster skim over the top.
Construction for Masonry cavity wall
Now for a masonry cavity wall, outside to in…
Outer leaf
We’ve got our brick again on the outside, just like timber frame
Cavity and Insulation
Then our cavity, and this time we need a minimum 80mm of cavity insulation so a bit more than the timber frame, for Scotland it should be 90mm to comply with their stricter regulations, add to our 50mm cavity and we get 130mm total.
Blockwork inner leaf
This sits against 140mm thick blockwork, secured using these wall ties with plastic clips,
Since we never want the insulation to move and start to bridge the cavity
Dot Dab plasterboard and 3mm skim coat plaster
Then, on the inside of the blockwork, we have the option of full coat 15mm plaster, or the” dot dab” method….12.5mm plasterboard sheets (drywall) with big dollops of adhesive behind, and skim coat over. You can also use Aimes taping instead of a skim coat.
I’ll always go dot dab, which means I can use drywall boxes for my electrical work and run my cables in the void. Drywall boxes always so much easier than metal back boxes.
Full coat plaster saves you a little floor space, but it’s more hassle to do your cabling and back boxes, which need to be cut into the blockwork in order to sit flush.
Difference between Timber frame construction and brick block cavity wall – labour and material costs?
Really, there’s not a lot of difference in cost, nor is there much difference in time. See my other cost comparison post for a detailed breakdown.
It’s just the materials that make the difference. I’ll leave a link to the pricing and material files shown in that post, so you can play about with them for your own project.
My five key factors for Timber Frame v Masonry Block Cavity Wall
1. We need to consider drafts ….or Air Tightness
It’s much easier with timber frame to get that tightness, since you’re using a combination of a vapour barrier and a breather membrane. For a cavity wall, you’re relying on taping the foil in the cavity if you’re not using plasterboard, difficult to maintain full air tightness at all the awkward junctions.
2. Cavity alone v cavity with breather membrane
In a traditional cavity wall, you only have air cavity to provide the water barrier element,….. in a Timber Frame construction, is the air cavity supplemented by the breather membrane, so you get a much higher level of moisture and damp barrier one way, whilst allowing the building to breath the other way.
3.Convenience and speed
I want to avoid scenarios where I’m getting held hostage to broken promises on dates because masonry trades are just so inundated with work at the moment…..if you’re self building the timber frame element, or working with a joiner or carpenter, you can get the whole thing wind and watertight, roof on, windows and doors in and sealed, without having to wait on your brickie. The outer brick leaf can go on pretty much anytime. so timber frame is a massive advantage for streamlining the trades.
4. Space for services
In a traditional cavity wall there’s No space for services, dot dabbing with skim is ok but increases wall thickness, and so you’re losing floor area, it’s more expensive that plastering, and there’s still no room for heating pipes with pipe insulation. Timber frame solves all of that.
5. For timber frame I’ve got the Flexibility of a range of rain screens
the outer cladding, facing bricks, but also cedar, render board for a rendered aesthetic, composure cladding, or a mixture. You can’t easily do that with masonry, outer leaf has to be either facing brick or render.
Overall, the only real benefit for these small projects I see for traditional brick and block cavity wall over timber frame construction for your home build project or house extension is where…
You’re also using concrete ground slab
Since it is straightforward to get a DPM and DPC down and then immediately continue to lay the blocks and bricks onto the trench blocks. However you then need to factor in the additional engineering for designing and pouring a concrete slab and the reinforcement that goes with it
Just a single trade can do the founds, the slab and the masonry
a couple of builder bricklayers do founds, ground slab, walls up, insulation in, openings formed with lintels to roof level in super quick time, since there’s just the one trade involved. However these days it is now very difficult to find squads that can do these combined trades, they tend to focus on a single aspect to maximise economy
Traditional brick and block cavity wall construction
Most of us understand how a cavity wall works since it has been around for such a while. Timber frame technology and construction, although incredibly simple and easy for the self builder, can still seem a little mystifying at first. Hopefully the explanations here will help
Combustibility
Masonry is non combustible and therefore there are no problems building up to a boundary of your property. With timber frame, there are some additional steps we need to consider
Timber Frame or Masonry Cavity Wall
The Right Construction for your project ?
Timber Frame Pros
Air Tight
We need to consider drafts. Air Tightness is easier
Breath
Addition of a breather membrane moisture control
Speed
Faster to wind and watertight and less trades involved
Space
Less thick wall makeup than masonry and service zone
Brick and block cavity wall Pros
Concrete slab
Works well with ground bearing concrete slab
1 trade
Bricklayers do founds, ground slab, walls up, insulation
Familiar
Easier for some people to understand as traditional
No fire issues
Steel and lintels can be easier to set in for the less experienced
Overall, the only real benefit for these small projects I see for traditional brick and block cavity wall over timber frame construction for your home build project or house extension is where…
- you’re also using concrete ground slab
- and a couple of builder bricklayers do founds, ground slab, walls up, insulation in, openings formed with lintels to roof level in super quick time
- there’s just the one trade involved.
- Then joiners come in
but… It’s much harder to find teams to do that nowadays and, you’re giving up control of the setting out.
Some final thoughts on why you might want to opt for brick and block cavity over timber frame construction…
Timber frame Cons
My advice for the self builder and competent DIYer – always go for timber frame
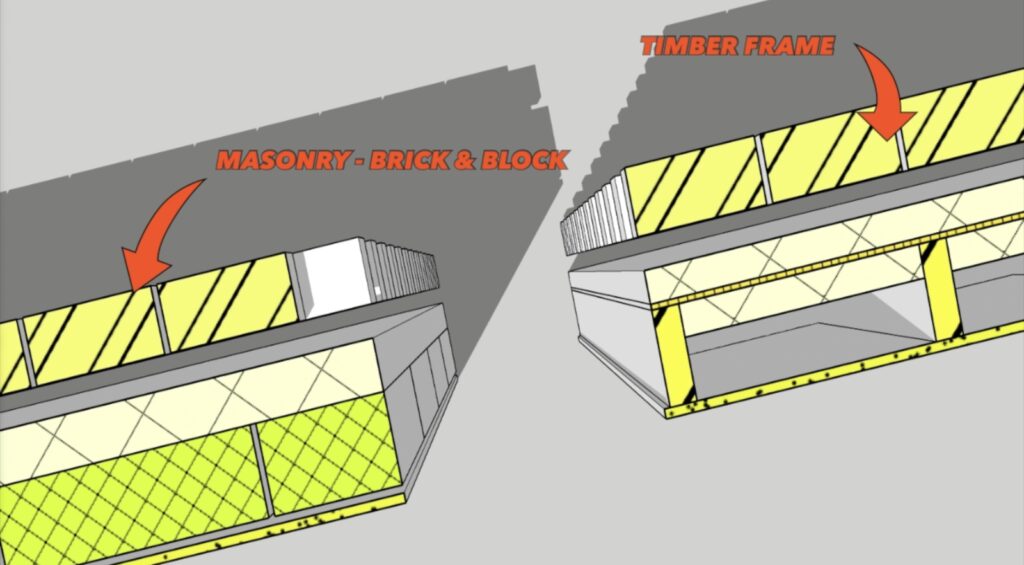
Frequently Asked Questions – Timber Frame v Masonry
Conclusion – Timber Frame or Masonry Cavity Wall? What is best?
I’ll always go for Timber Frame for these small house extension projects, me and my colleagues work as multi tradesmen, running cables, joinery work, fitting windows ourselves, like any typical self builder.
Leave a comment if you have any questions, or you have had a different experience, and call me if you need further more detailed advice for your project. Best of luck.